
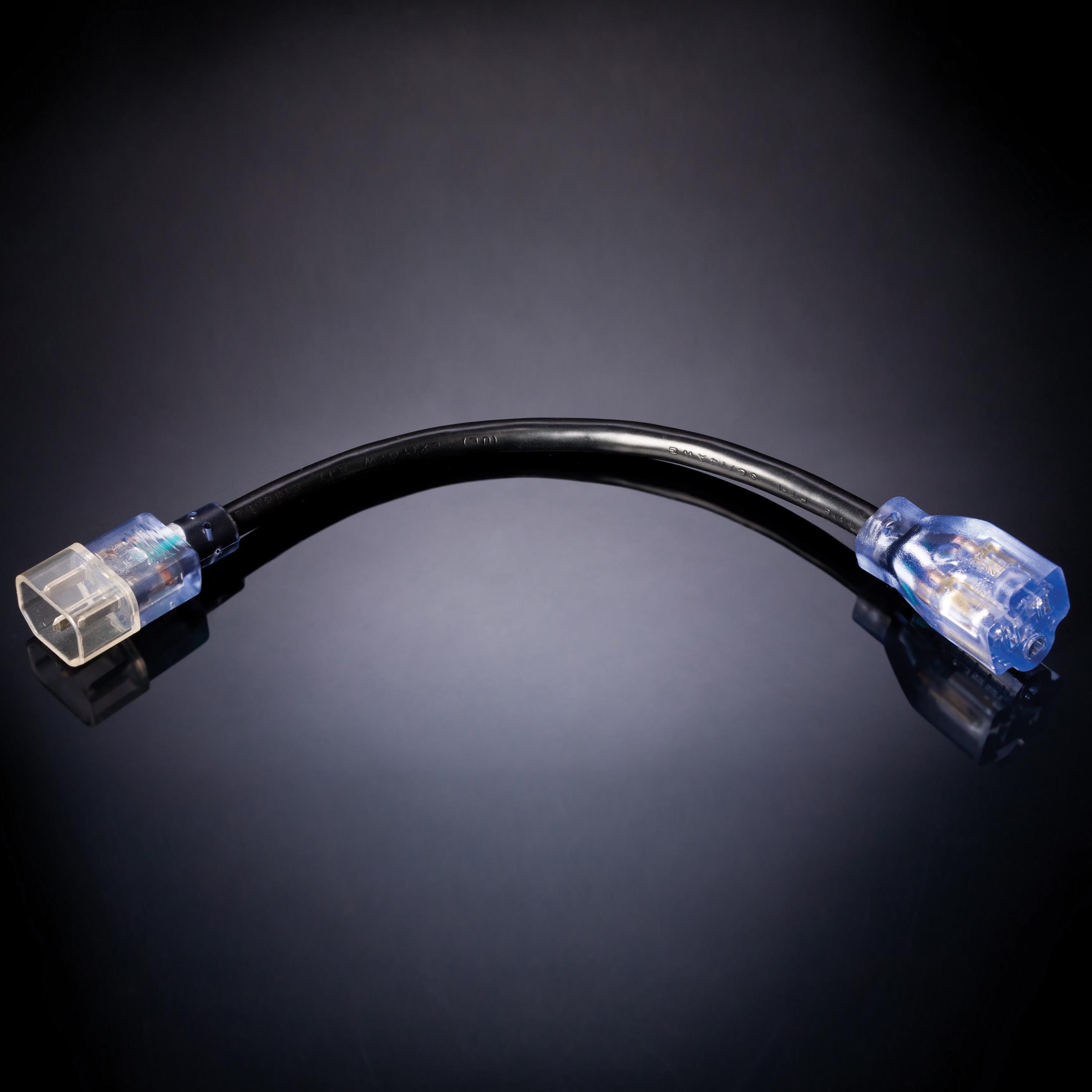
Having a reliable board-in board or IC test socket is extremely important so they don’t fail during test phase. The burn-in board design is pretty similar to standard PCB guidelines, but additional elements need to be considered. At Abrel Product we constantly work on our designs and focus on innovation to meet the needs of our clients. One of the challenges facing burn-in board manufactures is keeping pace with a rapidly moving industry. Abrel completes over 200 Burn-in board design projects per year. Our design engineers use Seetrax Ranger CAD workstations, which are optimised for efficient burn-in board design. The boards that Abrel produce can be tailored for all system types and a wide variety testing conditions including HAST, LTOL, *85/85 and HTOL.
#Burnin board free#
We also use high temperature lead free solders and stainless-steel board fixtures. For temperatures over 250☌ a higher grade of polyimide is used. Generally speaking we use IS410 for applications up to 155☌ and polyimide for applications up to 250☌. Once the stress tests have been completed engineers will analyse the results to make sure everything is working within the correct parameters.ĭuring the burn-in process extreme temperatures often ranging from 125☌ – 250☌ or even 300☌ are applied so the materials used need to be extremely durable. The components added to the board are stressed using extreme heat to highlight any failures. The BoardsĪ burn-in board is a printed circuit board that is used in the burn-in process. The component will then be operating in the useful life phase. By elevating the temperature during test the failure mechanisms are accelerated to eliminate any early device failures. The nature of semiconductors is that many failures occur during the early stages of operational life (infant mortalities). The typical lifespan and early failure rates of semiconductors can best be illustrated by the ‘Bathtub Curve’ as detailed in the diagram above. This ensures the manufacturer can be confident they have a robust end product. Very often the semiconductor components are pushed beyond what they will have to go through in reality to allow for additional headroom. The tests that are run will try to trigger possible failures that could happen in the real world and improvements can be made if necessary. Burn-in Processįirst of all, ‘burn-in’ is a process where semiconductor components are stress tested in order to detect any early failures due defects in design, materials, process or manufacturing. So, we thought we’d explain them for you in a little more detail…. We’ve been making burn-in boards for Semiconductor companies all around the world since 1994 -it’s like second nature to us. In the PCB industry the term ‘Burn-in Board’ is very common but if you’re just getting into the industry you might be scratching your head a little as to what one is!
